Young Manufacturing YM Factory Tour
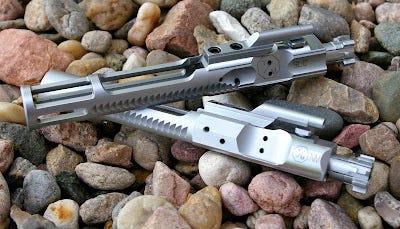
Young Manufacturing YM Factory Tour
Making the Best AR Carriers in the World
During a recent trip to the Pheonix area, I was fortunate to be provided a personal plant tour of Young Manufacturing by Dan Young himself and it was stunning how much work goes into making just the Carrier and complete Bolt Carrier Group. But first let’s look at what this critic…
Keep reading with a 7-day free trial
Subscribe to Major Pandemic - MajorPandemic.com to keep reading this post and get 7 days of free access to the full post archives.